Altech to Commercialise 120 MWh Sodium Chloride Solid State Batteries for Grid Storage
Altech Batteries Limited has executed a joint venture agreement with leading German battery institute, Fraunhofer IKTS (“Fraunhofer”) to commercialise the Sodium Chloride Solid State (SCSS) Battery. Altech will be the majority owner at 75% of the joint venture company (Altech Batteries GmbH) and will be commercialising a 120 MWh project to be situated at the site in Schwarze Pumpe, Saxony, Germany. SCSS batteries brand name CERENERGY® Battery uses high purity alumina for the critical ceramic solid state electrolyte which is a strong link to Altech’s core business and competency.
Definitive / Bankable Feasibility Study
A Definitive Feasibility Study (“DFS”) on the CERENERGY® 120 MWh project was completed in March 2024 that included compelling economics, even at this relatively small first production line capacity. The vision and strategy for the CERENERGY® project is to reach gigawatt capacity, and Altech has the worldwide rights of manufacturing, licensing and distribution of this product.
Watch video of CERENERGY® Battery DFS Announcement
DFS – Project economics
With a capital investment of €156 million and working capital of €23 million, Altech’s DFS predicts a net present value (NPV9) of €169 million and annual EBITDA of €51 million from operations. The estimated internal rate of return stands at 19%, with a steady state capital payback period of 3.7 years. At full production capacity of 120 1MWh GridPacks, the expected annual revenue is €106 million, boasting an EBITDA margin of around 47%. Considering the projected growth of the grid storage market at 28% CAGR, Altech Batteries Limited and its joint venture partners have approved the funding phase (Final Investment Decision) for this project.
The Project
Sodium Chloride Solid State (CERENERGY®) batteries (also known historically as sodium nickel chloride batteries) will be the grid battery storage of the future. The CERENERGY® technology has been developed by Fraunhofer IKTS for the last eight years and has revolutionised previous technology, allowing higher energy capacity and lower production costs. The world‘s largest CERENERGY® type batteries in terms of capacity has already been successfully tested in stationary battery modules. The Fraunhofer CERENERGY® batteries are in the final phase of product testing and ready to commercialise. Fraunhofer have spent in the region of EUR 35 million in research & development and operates a EUR 25 million pilot plant in Hermsdorf’, Germany (See Figure 11).
Fraunhofer have been searching for an entrepreneurial partner who has German land available; has access to funding; a builder of projects; a battery background and has technology in alumina used in ceramics. Altech fitted the criteria, and the joint venture was formed. Altech group will own a majority (75%) of the project with Fraunhofer (25%) free carried. The intellectual property will be licensed exclusively to the joint venture.
The joint venture has elected to develop a 120 MWh CERENERGY® battery plant (Train 1) on Altech’s site in Saxony, Germany. The target market is specifically focussed on the grid (stationary) energy storage market which is expected to grow by 28% CAGR in the coming decades. The global grid energy storage market is expected to grow from USD 4.4 billion in 2022 to USD 15.1 billion by 2027. Or further out, growth is expected from 20 GW in 2020 to over 3,000 GW by 2050. CERENERGY® batteries can provide high security at low acquisition and operating costs for stationary energy storage market.
The joint venture has commenced the planning process for the bankable feasibility study required for the commercialisation process. Once the Train 1 (120 MWh) plant is built and operating, the longer-term vision for the joint venture is to consider additional trains or a Gigawatt battery facility in Saxony.

Altech has designed and launched the CERENERGY® Sodium Alumina Solid State (SAS) 60 KWh battery pack (ABS60) designed for the renewable energy and grid storage market. Based on preliminary discussions with potential off-takers for the 120MWh CERENERGY® battery project, the proposed battery module for 10 kilowatt-hours (KWh) has been superseded by a 60 kilowatt-hour (KWh) battery pack (ABS60) rated at a higher voltage of 600 volts and 100 amp hour (Ah). A video of the battery design can be seen on Altech web site or on YouTube https://youtu.be/OHPdGvaOlmI

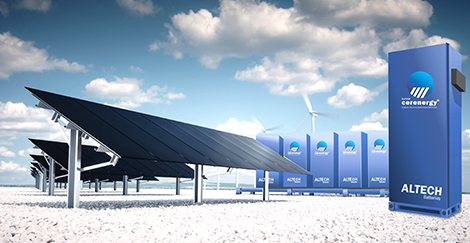
Altech has launched the design for the CERENERGY® Sodium Alumina Solid State (SAS) 1.0 MWh GridPack (ABS1000) destined for the renewable energy and grid storage market. Based on preliminary discussions with potential off-takers and to minimise on site installation of individual ABS60 60KWh battery packs, a pre-installed solution has been launched. Each GridPack will have up to twenty 60 KWh battery packs installed and connected to pack power management system. Every GridPack has a distinct rating of 600 volts DC and 100 Ah, and it can be arranged in series (cluster or array) to achieve the required rating of several thousand KWs for grid functioning. A video in relation to this can be viewed on Altech’s website.
Challenges with Lithium-ion batteries
Fire and Explosion Issues
One of the significant drawbacks of lithium-ion batteries is the risk of thermal runaway, fire and explosion which have been in the news recently. Today’s lithium-ion battery contains a liquid flammable electrolyte and a flammable plastic separator. Thermal runaway is a chain reaction within a battery cell that can be very difficult to stop once it has started. It occurs when the temperature inside a battery reaches the point that causes a chemical reaction (producing oxygen) to occur inside the battery. It is often caused by overheating, physical damage and over charging.
Narrow Operating Temperature Range
The other drawback is that they are required to operate in a relatively narrow temperature range which is between +15 oC to +35 oC. At lower temperatures, the liquid electrolyte in the battery becomes more viscous which slows the lithium transfer and reactions. A lithium battery at 0 oC will reduce a typical battery capacity down to 70%. This makes application of lithium-ion batteries in cold and desert climates extremely challenging. Often available battery energy is used in the heating or cooling of these batteries.
Lithium-ion Battery Lifespan
Thirdly, the life of lithium-ion batteries is still limited to between 7-10 years depending on application. Lithium ions degrades with each charge and discharge cycle. This deterioration is often due to detrimental side reactions, dendrite growth, and the breakdown of anode and cathode structures. This degradation is much faster when the battery is operated outside the ideal temperature range. For electric vehicles (EVs), manufacturers will guarantee a battery for around 8 years when the capacity of the battery drops below 70%. For grid storage batteries, a life span of 7-10 years can be expected. For grid storage, the storage costs taking account replacement costs is the long-term storage costs of a battery.
Lithium Costs and Availability
The global market for lithium is growing rapidly. The price of lithium which is the most critical component of a lithium-ion battery has risen six-fold since that start of the year. Lithium prices have spiked sky high, putting upward pressure on the production costs associated with lithium-ion batteries. The production of lithium is concentrated in four countries, namely Australia, Chile, China and Argentina. There is a real concern that there isn’t enough mines and production capacity being developed to meet the forecast demand for EV’s as well as stationary energy storage.
Cobalt Supply Chain and Ethical Concerns
Cobalt is key for boosting energy density and battery life because it keeps the cathode layered structure stable as lithium ions transfer into and out of the cathode during battery operation. Cobalt is considered the highest material supply chain risk for EVs in the short and medium term. EV batteries can have up to 20 kg of cobalt in each 100 kilowatt-hour (kWh) pack. Right now, Cobalt can make up to 20% of the weight of the cathode in lithium-ion EV batteries. The Democratic Republic of Congo (DRC) produces about 70 per cent of global cobalt and the lithium-ion battery industry is exposed to precarious supply chain issues. Stories of the harsh and dangerous working conditions, child labour and human rights abuses in the DRC has caused ethical concerns with cobalt supply.
Graphite Geo-political Risk
Graphite is thus considered indispensable to the global shift towards electric vehicles. It is also the largest component in lithium-ion batteries by weight, with each battery containing 20-30% graphite. But due to losses in the manufacturing process, it takes 30 times more graphite than lithium to make the batteries. The graphite deficit has started, as demand for EV battery anode ingredient exceeds supply resulting in price increases. Today China produces 90% of the world graphite anode material which represents a concerning geo-political risk to the industry.
Copper Crunch
Copper is mainly used as the current collector on the anode part of a lithium-ion battery. Copper is looming as the biggest worry, with the biggest driver of scarcity being the energy transition and increased EV demand. A recent report (Future of Copper) notes. “The 2050 climate objectives will not be achieved without a significant ramp-up in copper production in the near and medium term, which will be very challenging,” A battery electric vehicle requires 2.5 times more copper than a standard inner combustion emissdion (ICE) vehicle. There simply isn’t enough copper mines being built or expanded to provide all the copper needed to produce the 27 million EVs that S&P Global has forecast to be sold annually by 2030. Copper could rival oil as a national energy security concern for some countries.
The Ideal Battery?
Based on the above challenges facing lithium-ion batteries and the increasing prices of the critical materials and metals used in these batteries, is there a battery technology that resolves these problems? Is there a battery that is fire and explosion proof, has lifespan of more than 15 years, and operates in extreme cold and desert climates? Is there a battery technology available where it is lithium free, cobalt free, graphite free and finally copper free, which limits the exposure to soaring critical metal prices and supply chain concerns?
Introducing Altech’s Sodium Alumina Solid State CERENERGY® Batteries.
CERENERGY® batteries resolves some of the biggest problems and challenges facing lithium-ion batteries today.
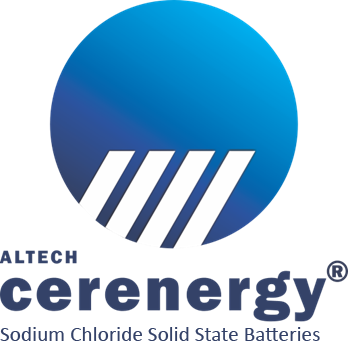
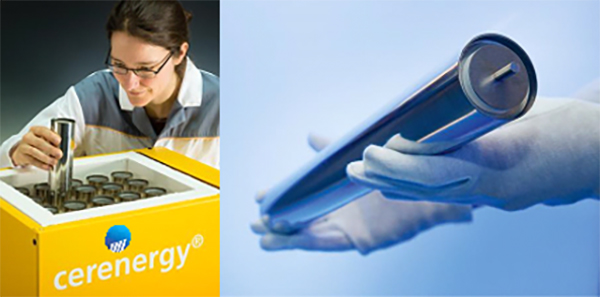
CERENERGY® Batteries are Fire and Explosion Proof
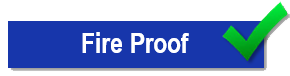
CERENERGY® batteries are totally fire and explosion proof and is not prone to thermal runaway which is one of the biggest advantages over lithium-ion batteries. Firstly, CERENERGY® batteries does not contain flammable liquid electrolyte or plastic separators; the electrolyte is a solid inflammable ceramic tube that allows sodium ions to transfer through it. Secondly, the battery, due to its chemistry does not contain oxides nor generate oxygen at the cathode like a lithium-ion battery does during thermal runaway. Being a much safer battery, it is ideal in indoor industrial and commercial energy storage installations. The battery is totally safe and does not react with water and is highly sort after for sensitive environments eg areas subject to flooding, where lithium-ion batteries are banned from these applications.
Large Operating Temperature Range – Cold and Desert climates
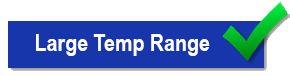
CERENERGY® batteries can operate efficiently between minus 20°C to +60 °C range and guarantee high performances and durability regardless of the ambient temperature. Because the CERENERGY® battery has no liquid electrolyte (solid ceramic electrolyte), ambient temperature does not adversely affect the performance of the battery. In addition, the CERENERGY® batteries are internally high temperature batteries (operates around 300 oC) but is fully insulated so the external of the battery module is at “human touch” temperature. The core temperature of the battery is self-sustaining and does not require cooling like lithium-ion batteries. They are ideal grid energy storage batteries for extreme cold and desert climates which is the main disadvantage of the lithium-ion batteries. For this reason, the CERENERGY® battery has it’s own specific market without any competition from lithium-ion batteries.
CERENERGY® Battery Life Span
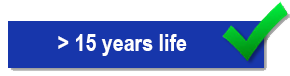
Unlike lithium-ion batteries, there are no sodium ion degradation with each charge and discharge. There is no first cycle loss, no detrimental side reactions, no dendrite growth, or breakdown of anode and cathode structures. The absence of liquid electrolyte replaced with solid ceramic means there is virtually no sodium deterioration in the battery. The life span of CERENERGY® battery is beyond 15 years. In a recent study by ITP Renewables, the CERENERGY® type battery did not show any deterioration in estimated state of health in the first 700 cycles of testing compared with the normal deterioration in LFP and NMC lithium-ion batteries. See Figure 0. CERENERGY® type batteries have been reported with lifetimes of over 2,000 cycles and more than 15 years have been demonstrated with full-sized batteries.
Figure 0 – Life span testing of various batteries including CERENERGY® type batteries
Lithium Free Battery
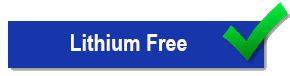
CERENERGY® batteries do not contain lithium but uses sodium ions from common table salt. In fact, the cathode consists of salt (sodium chloride) and nickel. Sodium is the next reactive alkali metal on the periodic table under lithium (Li is -3.05 V whilst Na is -2.7 V) and is equally ideal for energy storage in batteries. Salt is not a critical element, is many times cheaper than lithium and is readily available everywhere. CERENERGY® type batteries are also known as “sodium nickel chloride” batteries. CERENERGY® technology is different from sodium-ion batteries (has liquid electrolyte) or sodium sulphur (sodium sulphur instead of sodium chloride) batteries. CERENERGY® batteries are not exposed to rising lithium prices and potential supply constraints of lithium globally.
Cobalt Supply Chain and Ethical Concerns
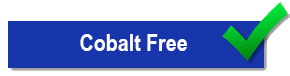
No cobalt is used in CERENERGY® battery. As mentioned previously, the cathode consist of salt and nickel in a sodium aluminium chloride medium. Due to the chemistry of the battery, there is no requirement for a cathode layered structure like lithium-ion batteries so there is no requirement for cobalt. CERENERGY® batteries have excellent specific energy of 110-130 Wh/kg compared to LFP lithium-ion battery of 90-160 Wh/kg. CERENERGY® batteries have no exposure to cobalt ethical or supply chain issues.
Graphite and Copper Supply Risks
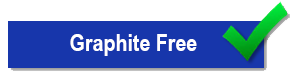
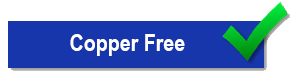
The other unique feature of the CERENERGY® battery is that it does not contain any graphite or copper in the anode side of the battery. In fact, there is no anode in the CERENERGY® battery. The anode only forms during the charging process as a molten sodium film between the steel electrode and outer edge of the ceramic electrolyte. Similarly, the molten sodium anode dissolves during the dis-charging process of the battery. Instead of copper as the negative collector in the lithium-ion battery, a steel canister acts as the negative electrode in a CERENERGY® battery. The CERENERGY® battery is graphite free, and copper free.



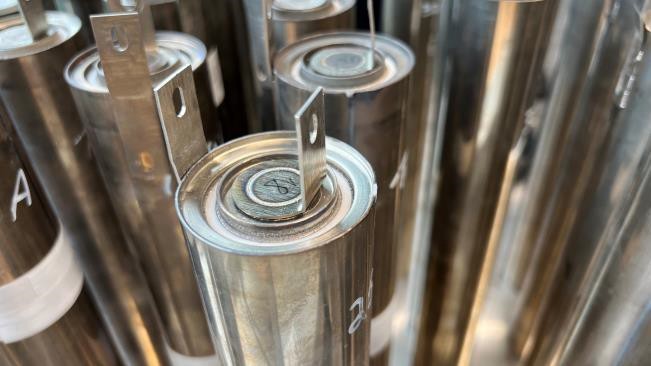
What is a CERENERGY® battery?
A CERENERGY® battery consists of a ceramic tube (conductive to sodium ions but insulator for electrons) with a positive terminal in the centre of it. (See Figure 5). The solid ceramic tube (solid state technology) performs the same function as a liquid electrolyte in a lithium-ion battery, allowing sodium ions to transfer through it. IKTS (a ceramics institute) has developed the solid-state technology to produce these large solid ceramic tubes with micro-structures that allow fast sodium ion transfer. The ceramic tube is filled with cathode granules consisting of common table salt and nickel. To ensure contact between the solid cathode granules and the ceramic electrolyte tube, the tube is flooded with sodium aluminium chloride medium.
The ceramic tube is housed in a steel canister which acts as the negative terminal, see Figure 6. The positive and negative terminal tabs are installed at the top of the cell for electrons transfer and connection to other cells. Each cell operates at 2.58V and a collection of 40 cells are installed in a refractory insulated module casing. Each module is rated at 10KWh and 100 aH. The technology highlights for CERENERGY® batteries are high specific energy; excellent performance and cycle life in harsh operating environments; ultra long battery life span and low environmental impact.

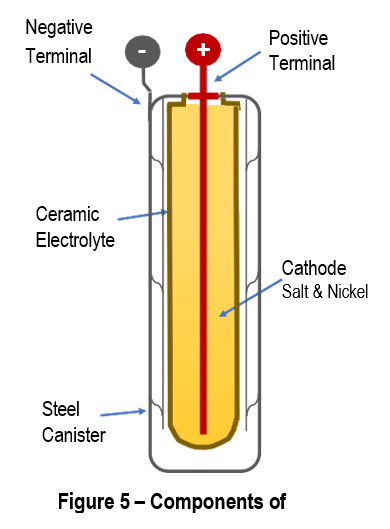
How the Battery Works
When the CERENERGY® battery is being charged, electrons flow from the positive terminal to the negative terminal. Sodium ions from the salt (sodium chloride) migrates through the solid ceramic electrode towards the negative canister terminal. The remaining chloride ions attach themselves to the nickel to form nickel chloride in the cathode medium. The sodium forms a molten anode layer on the outside of the ceramic tube, contacting the steel canister, (see Figure 7) and the battery is fully charged. During discharge, electrons flow back, molten sodium is oxidized into Na+ ions, and transfer back through the solid-state ceramic tube forming sodium chloride. Nickel chloride is reduced back metallic Nickel.
The electrochemical reaction of the battery is as follows:
Energy Density
The CERENERGY® batteries provides excellent performance in terms of energy and power density see Figure 9. The energy capacity is around 110- 130 Wh/kg and comparable to LFP lithium-ion batteries (90–110 Wh/kg). CERENERGY® batteries charge over 4-6 hours and discharge over similar times which is ideal for the grid storage market. Contrary to electric vehicle applications, batteries for stationary storage do not suffer from mass or volume constraints. However, due to the large amounts of energy and power implied, the cost per power or energy unit is crucial. The relevant metrics to assess the interest of a technology for grid-scale storage is the $/Wh (or $/W) rather than the Wh/kg (or W/kg). The joint venture believes that the CERENERGY® battery is ideally suited for the grid storage or long duration energy sector where very high power in a short period of time (like high power EV) is not required. The battery can be configured to meet greater than 600 V that is required in grid storage.
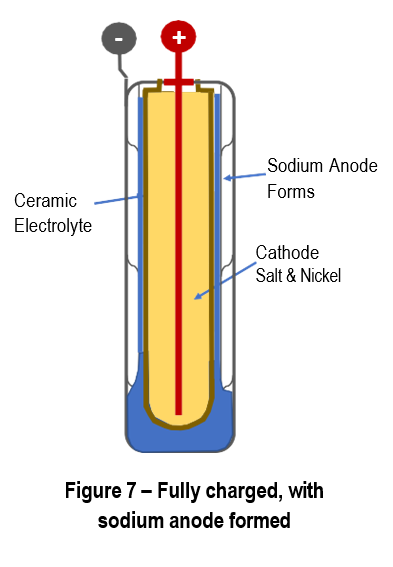
The battery plant will produce 1,666 battery packs per annum, rated at 60 KWh each. These CERENERGY® modules are expected to sell for between EUR 700-900 per KWh.







Grid Storage Market
Grid energy storage (also called large-scale energy storage) is a collection of methods used for energy storage on a large scale within an electrical power grid. Electrical energy is stored during times when electricity is plentiful and inexpensive (especially from intermittent power sources such as renewable electricity from wind power, tidal power and solar power) or when demand is low, and later returned to the grid when demand is high, and electricity prices tend to be higher. Developments in battery storage have enabled commercially viable projects to store energy during peak production and release during peak demand, and for use when production unexpectedly falls giving time for slower responding resources to be brought online.
Altech’s CERENERGY® batteries are targeted to supply to this grid energy storage market which is expected to grow by 28% CAGR in the coming decades. The global grid energy storage market is expected to grow from USD 4.4 billion in 2022 to USD 15.1 billion by 2027. Or further out, growth is expected from 20 GW in 2020 to over 3,000 GW by 2050.

There are several deployments of battery energy storage systems for large-scale grid applications. One example is the Hornsdale Power Reserve, a 100 MW/129 MWh lithium-ion battery installation, the largest lithium-ion grid storage in the world, which has been in operation in South Australia since December 2017. The Hornsdale Power Reserve provides two distinct services; energy arbitrage; and contingency spinning reserve. The facility can bid 30 MW and 119 MWh of its capacity directly into the market for energy arbitrage, while the rest is withheld for maintaining grid frequency during unexpected outages until other, slower generators can be brought online (AEMO 2018). In 2017, after a large coal plant tripped offline unexpectedly, the Hornsdale Power reserve was able to inject several megawatts of power into the grid within milliseconds, arresting the fall in grid frequency until a gas generator could respond. By arresting the fall in frequency, the facility was able to prevent a likely cascading blackout.
Details of Joint Venture Agreement
For the joint venture between Altech and IKTS, three agreements have been executed.
- Altech Energy Holdings GmbH and Fraunhofer Joint Venture (Altech Batteries GmbH) Agreement
- Research & Development Agreement between Altech Batteries GmbH and Fraunhofer
- Intellectual Property and Licence Agreement between Fraunhofer and Altech Batteries GmbH
Relevant Details in all Agreements
- Joint Venture Company – Altech Batteries GmbH (“ABG”)
- Ownership of ABG – AEH 75%, IKTS 25% free carried
- Ownership of AEH – ATC 75%, AAM 25% (see structure below)
- In exchange for the free carried interest of 25% of ABG, IKTS has executed an exclusive background intellectual property (IP) and know-how license agreement (“License“) to ABG
- ABG has no license royalties’ obligations for the first Train 1, 120 MWh project
- IKTS provides access to pilot plant, trials and technical expertise
- Altech Group will provide land for a Train 1, 120 MWh site in Saxony
- A service development contract has been executed to use IKTS services and personnel over a period of 4 years, to progress a DFS, funding, construction, commissioning and start up of the 120 MWh plant
- The service contract payment terms are commercially confidential
- During development, any IP (developmental, commercialization, product and marketing IP known as “foreground IP” developed will be property of ABG
- On completion of the DFS, if ABG decide to move to funding stage of the project, IKTS will be free carried
- ABG will have the right to use “CERENERGY® trademark for SAS batteries
- ABG will operate the 120 MWh battery business
- Once the pre-agreed IKTS service payment plan has been completed, the exclusive background IP will be owned by ABG
- At any time, ABG could proceed to expansion to Train 2 or Gigawatt Project (“Giga” Project)
- On completion of the Giga Project DFS, ABG may decide to fund the Giga project
- For the Giga factory case, IKTS can contribute to the equity component of the financing (own 25% of the Giga project) or covert the future ownership of the project to a background IP royalty agreement.
- The background IP royalty agreement will consist of 1.5% of product sales ex gate for all future sales of battery products.
- ABG by mutual agreement of both shareholders, could issue licenses to other parties.
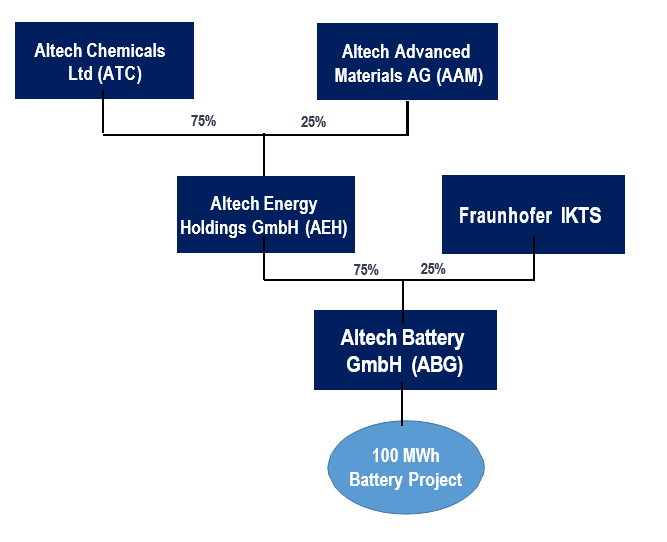
Fraunhofer IKTS Background
The Fraunhofer-Gesellschaft based in Germany is the world’s leading applied research organization. Prioritizing key future-relevant technologies and commercializing its findings in business and industry, it plays a major role in the innovation process. Founded in 1949, the Fraunhofer-Gesellschaft currently operates 76 institutes and research units with over 30,000 employees throughout Germany.
Fraunhofer Institute for Ceramic Technologies and Systems IKTS is one the 76 institutes which conducts applied research on high-performance ceramics. The institute‘s three sites in Dresden and Hermsdorf (Thuringia), Germany, collectively represent Europe‘s largest R&D institute dedicated to the study of ceramics. The annual budget of IKTS is € 83 million and has 800 employees. As a research and technology service provider, the Fraunhofer IKTS develops advanced high-performance ceramic materials, industrial manufacturing processes as well as prototype components and systems in complete production lines up to the pilot-plant scale
Green Bond Framework
Altech, in its efforts to access green bond finance for the CERENERGY® project, has prepared a Green Bond Framework to support a green project rating from intendent agency Standard & Poors. A copy of the Green Bond Framework can be accessed by clicking on the document link below.